First Promise, Then Pain, Now a Path Forward
October 24, 2018
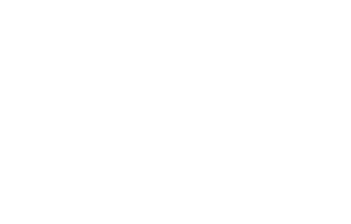
A Pragmatic Approach to Implementing Smart Factory Capabilities
The promise of increased efficiency, improved profitability, and new revenue streams from the adoption of smart factory capabilities is largely accepted as fact by manufacturers worldwide. According to a 2016 survey by the Boston Consulting Group of 750 industrial production managers, 85% of respondents indicated that they believe that they can benefit from implementing technologies from “the factory of the future,” with 74% already having implemented or planning to implement (within the next 5 years) some of these technologies.
What is driving this enthusiasm? According to Accenture, predictive maintenance could eliminate up to 70% of breakdowns in manufacturing and reduce overall maintenance costs by up to 30%. Those types of results are pretty exceptional, and it’s made an impression on executives around the World.
Enthusiasm, But Often Not Much Progress
At the same time, the willingness or ability to successfully implement smart factory capabilities hasn’t kept pace with the high expectations.
For example, only 9% of the 200 manufacturing organizations included in the 2018 Sikich Manufacturing & Distribution Report indicated that they are already using IoT capabilities in their plants. While you may see the smaller average size of these manufacturers as part of the reason that uptake is low (the median organization size was 101-250 employees), the statistics for larger organizations are also not stellar; in a 2018 survey of over 1,100 global manufacturing companies, PwC Strategy& found that 2/3 of companies have either barely begun or not started to implement the digital technologies of Industry 4.0.
But even for those that have started, the picture is also not rosy. The Boston Consulting Group survey noted above found that despite their enthusiasm, 25% of the organizations surveyed had not hit their targets for implementing smart factory technologies.
What’s Causing Efforts to Stall?
Frequently the organizations that have proceeded have begun efforts by pursuing pilot projects or Proofs of Concept (PoC). These smaller-scale projects are designed to create a model for implementation or prove out ROI assumptions before a company scales its implementation. It’s a smart approach to pick a focused effort on a smaller scale, but success has still been elusive.
According to the World Economic Forum, 70% of organizations pursuing IoT initiatives are stuck in the Proof of Concept (PoC) phase, otherwise known as “pilot purgatory.” The study, conducted in collaboration with McKinsey & Company, found even more astoundingly that 84% of companies were stuck in pilot mode for more than a year, and 28% for more than 2 years. The reasons for this project limbo were summarized as “too few resources, too little knowledge, and hard-to-justify investments for scale-up” in an article by McKinsey expert Enno de Boer.
A Cisco survey in April 2017 netted similar results, citing the top 5 challenges to successful implementation as time to completion, limited internal expertise, integration across teams, budget overruns, and (unique to their report) quality of data. [McKinsey did note in their top-line summary that “one company couldn’t perform analytics on its equipment because it didn’t own the data.” ]
However there was some good news to report beyond the depressing statistics. Both studies concluded that companies that build a strong partner ecosystem, rather than trying to go things alone, have a much greater chance of success that those that don’t take this approach. And 64% of the Cisco respondents indicated that the learnings gained from their failed projects has led to an acceleration of investment in IoT capabilities.
Reluctance to Dive In
These tales from PoC purgatory have definitely weighed on the organizations who’ve opted not to start yet. In addition to the staggering overall numbers serving as a cautionary tale, surveys of these laggard companies cite technology skills gaps and financial concerns – whether overall cost or inability to project an acceptable ROI – as barriers to adoption similar to their stalled counterparts.
But the eye-opening addition in virtually every survey, including a March 2018 report from Capgemini, is that firms who haven’t started are also very concerned about cybersecurity. At the same time, according to results from the Sikich report, only 19% of respondents classified themselves as “very ready” to address cybersecurity risks. This mismatch between the high level of concern with a low level of skills and tools is significant in holding companies back from starting with IIoT.
How to Get Started a Different Way
So where does that leave most manufacturers? How do they chart a different course forward?
We believe getting started doesn’t have to be hard, take a long time, or require a huge investment. This means taking an even smaller-scale approach than most current PoCs. In fact, it’s often better when manufacturers approach smart factory capabilities incrementally. As Canonical’s Tom Canning asserts in a May 2018 IndustryWeek article, the IIoT’s “real potential lies not in a radical rip-and-replace overhaul strategy but through incremental smart upgrades and improvements.”
And we couldn’t agree more.
That’s why we’re embarking on a series of posts that illustrate our experience implementing focused, practical, secure IIoT solutions with our clients. These are solutions that don’t boil the ocean. They focus on a specific challenge in the manufacturing environment. They are implemented with trust and security built into the solution. And they don’t cost hundreds of thousands of dollars to implement. Frequently the starting point is not even in the five-figures range.
These are practical solutions that solve a real problem and yield measurable ROI in months, not years.
Our next post will detail some use cases where video is added to the production environment. We’ll take you through the business issues, and the projected impact of an initial deployment.
Then we’ll follow that with a blueprint article that explains how to do it, from the shopping list of hardware, software, and supplemental items you’ll need, to a detailed explanation of how to put it all together.
And we’ll follow our video story with a second use case on monitoring auxiliary equipment on the plant floor. Again we’ll have two articles addressing the use case and business drivers in the first, followed by a blueprint for implementation in the second article.
Hopefully we have your interest piqued. Please stay tuned!
This is the first in a biweekly series of blog posts that will extend through the end of 2018. Please stay tuned and sign-up to subscribe to get our lasted content.
The second and third posts in this series are now available here:
Related articles
We were very excited to learn on Friday that the Corlina System of Trust has received a 2019 IoT Evolution Industrial IoT Product of the Year Award from IoT Evolution World, the leading magazine and Web site covering IoT technologies. It’s very exciting when your product receives this type of
In our recent articles, we’ve talked about taking a different approach to embarking on building IIoT capabilities, one that protects organizations from pilot purgatory by focusing on a specific challenge in the manufacturing environment and yielding ROI quickly. It’s not a rip-and-replace method requiring massive investments in new equipment. It’s
Solution Overview Corlina’s brownfield monitoring solution blueprint is intended to enable monitoring and decision-making based on information captured from already-in-place equipment. These existing systems are often implemented on closed architectures and/or closed data buses for reliability reasons, or they may not include any embedded sensors whatsoever. Corlina provides a cost-effective