When to Add Cameras to the Factory Floor
November 7, 2018
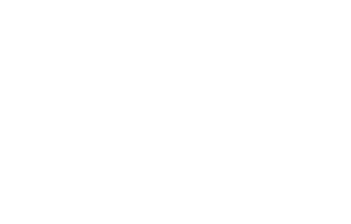
Adding cameras – whether video or still – to your production facility may be a great way to begin creating a connected environment, particularly if you’re struggling with an installed base of non-depreciated brownfield equipment or a process that includes significant manual work or assembly steps. Cameras offer lots of flexibility to record activities, provide a visual check on quality, or verify processes for reporting purposes.
Cisco’s Meraki published a set of innovative suggestions for using existing security cameras late last year, meaning if you have networked cameras on-hand that aren’t being used elsewhere, you may not even need to purchase all new equipment.
Cameras can be particularly effective at addressing specific business challenges such as new staff training, remote monitoring, production quality, or manufacturing safety. But is video really valuable enough to provide a return vs. solving the problem with other methods? In several cases, video can serve a unique role that other methods for solving the problem may not (or perhaps cannot).
So let’s get into some of the use case details.
Training
According to the third Skills Gap study conducted by Deloitte and the Manufacturing Institute in 2015, of the projected 3.5 million new manufacturing jobs being created in the U.S. by 2025, approximately 2 million will go unfilled due to the skills gap. This is the continuation of a trend that began over the course of the past decade, so if you’ve been managing a manufacturing facility for several years, you may be well aware of this already.
A big factor in the overall number of jobs to be filled, according to the study, is a looming 2.7 million retirements. Many of these soon-to-be retirees have worked in their organizations for years, if not decades. Their knowledge of manufacturing processes — even in environments where techniques are being updated with automation and other new technologies — is not something that can be easily replaced and definitely not learned overnight.
So how do you guard against the sudden loss of these valuable workers? Capture their work via video.
This all makes sense, right, but how do you really go about doing this? Unless you’re willing (and your older workers are too), having them wear a GoPro throughout the day is probably not a practical answer. You’ll either end up with thousands of hours of video you’ll never use or cameras that are mostly left off because it’s not second nature to turn them on at critical moments.
The better option is to focus on critical areas of the manufacturing floor, whether that’s a particular control station, or a touchy mechanism that needs frequent adjustment. Video recognition software can help you zero in on the right sections of footage for use in training or even machine diagnostics.
Quality Monitoring
Another excellent option for video is tracking product quality. There are multiple scenarios where video can be useful.
Manual processes:
If your production operation includes either manual assembly or any type of part creation or manipulation, having a video record of these processes can help you track and improve upon your product quality. Our customer, Hitachi High-Tech, is using cameras to track work conducted at work stations that cut bars for use in elevator cars, among other tasks. While their goal is remote management of these activities from their Japan headquarters, the video records are also helping the local staff improve upon their techniques and track production quality.
Assembly stations:
One modern area of camera use is imaging for Quality assurance. At Hitachi’s Thailand factory, they use cameras to compare the desired final assembly to what the production line has produced. Any errors can be picked up and rectified at this stage.
Another example is to use high quality imaging at various stages of production that compare the actual state with the desired state and allows the user to reject, and fix production issues early in the process so that wastage is kept at a minimum level.
If you are bringing together multiple elements, some or all of which may be externally sourced, a visual inspection and record of these parts coming together may prevent you from using pieces that don’t meet overall quality standards. This is particularly important in the production of complex items where the final product is constructed from multiple subassemblies. If either raw parts or subassemblies that don’t meet quality standards can be diverted before final assembly, scrap and rework costs can be significantly reduced.
Ingredient mixing / raw material addition:
Finally, if you are a food or cosmetic manufacturer, bringing together numerous ingredients, mixing stations are a great spot for cameras. Here video can document when a particular lot of an ingredient is added, verify that proportions are maintained, or otherwise provide a record of the integrity of your final product composition.
Remote Monitoring & Compliance
Remote monitoring, while desirable for organizations with multiple locations, may not be valuable enough in and of itself to spur the use of cameras. But add in the requirements of compliance reporting, and the scales may tip to favor the implementation of video or still images on the factory floor.
In a new engagement, we learned of the compliance requirements of a company with manufacturing facilities in North America and headquarters in Europe. The operational units must take regular measures at different production stations and report their results to HQ. Because the measurements take time to gather, management is looking to have a visual, time-stamped record of the measure, rather than just providing the data electronically. This ensures that all testing is done rigorously at the correct time intervals.
We also believe Compliance will be a growth area for IoT, with global insurance companies like Munich Re getting into the game with their acquisition of IoT middleware provider relayr. According to TechCrunch, “Insurance giants… have a clear strategic interest in IoT — with the technology… offering transformative potential for the insurance industry as data streams can be used to monitor equipment performance and predict (and even steer off) costly failures.”
Important Considerations When Using Video
If any of your video use cases capture the activities of employees, where they are identifiably captured in the video itself, you need to be aware that many localities regulate how these videos may be used and who can have access to them. In the U.S., these laws and regulations are typically implemented at the state level, so be sure to consult your business counsel.
Employee confidentiality was a key concern for Hitachi High-Tech, and a key reason for choosing Corlina as part of their solution. In their implementation, there is tracking to ensure that the captured video streams are only viewed by the appropriate personnel in the organization, and video streams are tracked from the collection point on the factory floor to their destination in the appropriate storage repository.
Getting Started
These use cases demonstrate just how versatile using cameras in your operational environment may be. One of the best arguments for trying video is that it’s easy to experiment because various video solutions have become so affordable and easy to operate.
If you’re intrigued by the opportunities, be sure to read our next post, “How to Add Connected Cameras to the Factory Floor,” to see how you can get started very simply.
This is the second installment of our blog series, A Pragmatic Approach to Implementing Smart Factory Capabilities. Be sure to read our intro article here.
Related articles
We were very excited to learn on Friday that the Corlina System of Trust has received a 2019 IoT Evolution Industrial IoT Product of the Year Award from IoT Evolution World, the leading magazine and Web site covering IoT technologies. It’s very exciting when your product receives this type of
In our recent articles, we’ve talked about taking a different approach to embarking on building IIoT capabilities, one that protects organizations from pilot purgatory by focusing on a specific challenge in the manufacturing environment and yielding ROI quickly. It’s not a rip-and-replace method requiring massive investments in new equipment. It’s
Solution Overview Corlina’s brownfield monitoring solution blueprint is intended to enable monitoring and decision-making based on information captured from already-in-place equipment. These existing systems are often implemented on closed architectures and/or closed data buses for reliability reasons, or they may not include any embedded sensors whatsoever. Corlina provides a cost-effective