Trust in the Smart Factory
March 19, 2018
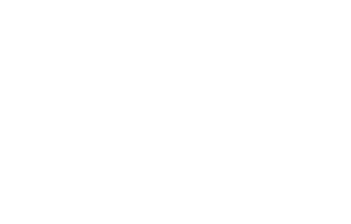
What Is the Meaning of “Trustworthiness”?
Many (large) manufacturers have jumped in with both feet to Industry 4.0 / IIoT projects, lured by the promise of returns from improved efficiency, reduced downtime, and the like. The focus has been on connecting the applicable equipment, largely via sensors, to applications, typically in the Cloud, that help predict maintenance needs or balance production schedules. The promised gains can be huge, not just financially, but also culturally and even in gaining a reputation as an innovator with partners and customers.
The problem, however, is that when companies focus on the big numbers and big headlines, they’ve often overlooked some decidedly “non-sexy” aspects of getting things right, the largest of which is making the system trustworthy.
The obvious thought that comes to mind when defining Trust is security, and of course those manufacturers implementing solutions should have their security software and policies in order! There are two complications: 1) security on the factory floor is exponentially more difficult than on the corporate LAN due to the increased attack surface created by the array of connected devices, and 2) security is just one component of Trust.
Security – Not the Whole Picture
According to the Industrial Internet Consortium or IIC, the trustworthiness of an IoT system is “the degree of confidence one has that the system performs as expected with characteristics including safety, security, privacy, reliability, and resilience in the face of environmental disruptions, human errors, system faults and attacks.”
This is a tall order for system owners, and it’s not solved with one simple recipe. What may adequately address safety or privacy in a manufacturing IoT system may be totally inadequate in a health care-related IoT implementation, for example. The different needs are fairly intuitive but the solutions are far more complex.
Where Do Resiliency and Reliability Come In?
Let’s go back to our theoretical manufacturer. In the scenario outlined, a manufacturer might connect machine sensors to an existing factory LAN or perhaps add Raspberry Pi-based cameras to the floor, connecting them via an available WiFi connection. The focus is on setting up data collection points, and then connecting them with the applications that provide the intelligence to reap the desired returns. And doing so quickly using existing infrastructure so as not to disrupt the operations on the factory floor. Perhaps even security has been addressed via technology, such as additional firewall protection, and access control, including specification of which people are authorized to view and download the collected data.
But what happens to the system when there’s a power outage? In all likelihood, the plant has an emergency generator which kicks in after a few seconds keeping the operation up and running. However, if the WiFi router hasn’t been connected to the generator, perhaps the cameras, which may be working, aren’t able to send data to the Cloud. The system hasn’t been able to respond with resiliency to the current disruption.
And lack of reliability can have a similar impact. If a connection is intermittent or a sensor is offline, the results of the high-profile predictive maintenance project could be compromised. It may not be obvious at first, because results are moving in the right direction. However, the full impact of the program at hand will never be realized if 100% of the data cannot be relied upon as accurate or complete.
The Implications of Trustworthiness
Just as the definition of trustworthiness encompasses so much more than security, its implications are also broad. A trustworthy Smart Factory ensures asset integrity, process integrity, and data integrity. And no one-size-fits all solution, or even a single platform solution, exists to support manufacturers in achieving the goal of trustworthinessgetting there involves using an appropriate multifaceted solution involving multiple components.
Taking on this challenge may be daunting, but as groups like the IIC develop reference architectures and new vendors with innovative solutions reach the market every day, companies will be able to implement an appropriate solution for their production environment enabling them to meet their business goals. The time is now for all manufacturers to benefit from the value of IIoT, not just the big guys with the big budgets.
Subscribe to Smart Factory News, the Corlina blog to read more on trust in the Smart Factory. And stay tuned for our upcoming white paper on how we help manufacturers of all sizes achieve Trust in their Smart Factories.
Related articles
We were very excited to learn on Friday that the Corlina System of Trust has received a 2019 IoT Evolution Industrial IoT Product of the Year Award from IoT Evolution World, the leading magazine and Web site covering IoT technologies. It’s very exciting when your product receives this type of
In our recent articles, we’ve talked about taking a different approach to embarking on building IIoT capabilities, one that protects organizations from pilot purgatory by focusing on a specific challenge in the manufacturing environment and yielding ROI quickly. It’s not a rip-and-replace method requiring massive investments in new equipment. It’s
Solution Overview Corlina’s brownfield monitoring solution blueprint is intended to enable monitoring and decision-making based on information captured from already-in-place equipment. These existing systems are often implemented on closed architectures and/or closed data buses for reliability reasons, or they may not include any embedded sensors whatsoever. Corlina provides a cost-effective